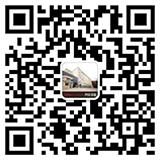
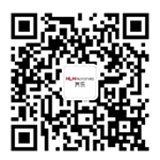
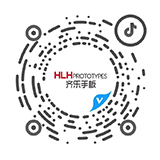



2025-04-23 13:42:04
CNC加工的表面粗糙度Ra值取决于具体的加工方式、刀具选择、切削参数以及材料特性等因素。以下是CNC加工中常见的表面粗糙度范围及影响因素:
数控车削粗车:Ra 20-10 μm半精车/精车:Ra 1.6-0.8 μm镜面车削(如金刚石刀具高速加工有色金属):Ra 0.04-0.01 μm。
数控铣削粗铣:Ra 6.3-2.5 μm精铣:Ra 1.6-0.63 μm超精铣(如高转速、小进给):Ra 0.4 μm。
数控镗削普通镗孔:Ra 2.5-0.63 μm精镗:Ra 0.32-0.08 μm。
磨削加工精密磨削:Ra 0.16-0.04 μm超精密磨削:Ra <0.01 μm。
CNC加工中通常以以下Ra值作为标准选项,适用于不同场景:
Ra 3.2 μm:默认经济等级,适用于一般消费类零件,表面可见轻微刀痕,适合轻负载、低速运动部件。
Ra 1.6 μm:用于紧密配合或受力零件,如滑动导轨、低速旋转轴,需高速切削和细进给。
Ra 0.8 μm:高等级表面,适用于轴承、高应力集中区域,成本增加约5%。
Ra 0.4 μm:超精细表面,用于高精度轴承、医疗植入物等,成本增加约11-15%。
刀具与切削参数:刀具刃口精度、转速、进给量直接影响表面质量。高速切削配合细进给可降低Ra值。
材料特性:有色金属(如铝合金)易实现低Ra值,钢材需更高工艺控制。
后处理工艺:抛光、喷砂等可改善表面光洁度,但可能影响尺寸公差。
常规CNC加工:Ra值范围为Ra 0.4–3.2 μm,具体取决于工艺和需求。
高精度要求:通过镜面车削、超精密磨削等技术,可达到Ra <0.01 μm,但成本显著上升。
选择原则:根据零件功能、耐磨性、配合要求平衡粗糙度与成本,避免过度加工。
如需具体Ra值的实现方案,建议结合材料、设备性能及成本预算,参考ISO 4287标准或咨询供应商。