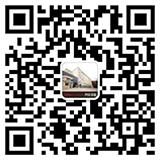
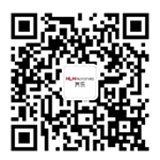
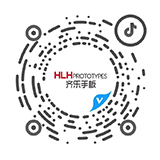



2025-02-25 13:43:24
CNC加工技术的要求涉及多个方面,以下是一些关键的技术要求:
1. 加工前的设计规划要求
精准的图纸设计:使用专业的CAD(计算机辅助设计)软件进行产品三维建模,确保设计的精确性和完整性。模型的尺寸精度、几何形状等需符合最终产品的要求,为后续加工提供准确的数据基础。
合理的工艺规划:工艺工程师要根据产品的形状、材料和加工要求,制定详细的加工工艺路线。包括确定加工工序的顺序,如粗加工、半精加工、精加工等的安排;选择合适的切削工具,考虑刀具的材质、形状、尺寸等因素,以确保加工效率和质量;确定切削参数,如切削速度、进给速度、切削深度等,不同的材料和加工要求需要匹配不同的切削参数。
2. 编程与模拟要求
准确的程序编写:利用CAM(计算机辅助制造)软件,将CAD设计的产品模型转换为CNC机床能够识别的G代码或M代码程序。在编写过程中,需考虑材料的切削性能、工艺的合理性等因素,保证加工过程的效率和质量。
程序的模拟验证:在实际加工前,通过CAM软件的模拟功能,对编写的加工程序进行虚拟加工模拟,检查刀具路径是否合理、是否存在碰撞干涉等问题,及时发现并修正程序中的错误。
3. 机床与设备要求
机床的精度与稳定性:CNC机床本身的精度和稳定性对加工质量至关重要。高精度的机床能够保证零件的加工精度,减少尺寸误差和形状误差。同时,机床的结构要稳定,具有良好的刚性和热稳定性,以抵抗加工过程中的切削力和温度变化。
设备的维护与校准:定期对机床进行维护和校准,包括检查机床的各部件是否正常运转、刀具系统的精度、坐标测量系统的准确性等。确保机床始终处于良好的工作状态,以保证加工精度的一致性。
4. 刀具与材料要求
刀具的选择与质量:根据加工材料的特性和加工要求,选择合适的刀具类型,如硬质合金刀具、陶瓷刀具、金刚石刀具等。刀具的精度、锋利度和耐磨性直接影响加工表面的质量,因此要选择质量好、精度高的刀具,并定期更换磨损的刀具。
材料的适用性:了解加工材料的性能特点,如硬度、韧性、热导率等,以便选择合适的加工参数和刀具。不同的材料对切削力、切削温度的反应不同,需要根据实际情况进行调整。
5. 加工过程的要求
装夹的准确性:工件在机床上的装夹方式和位置要准确可靠,保证工件在加工过程中不会发生位移或变形。根据工件的形状和尺寸,选择合适的夹具,并进行正确的装夹操作。
加工参数的控制:在加工过程中,严格按照预先设定的加工参数进行操作,包括主轴转速、进给速度、切削深度等。同时,要根据加工的实际情况,如切削力的变化、刀具的磨损等,适时调整加工参数,以确保加工质量和效率。
冷却与润滑:有效的冷却和润滑对于提高刀具寿命、减少切削力和防止工件过热变形非常重要。选择合适的冷却液和润滑方式,如浇注式冷却、喷雾冷却等,确保加工过程的顺利进行。
6. 质量检测与控制要求
在线检测:在加工过程中,采用在线检测技术,如激光扫描、多普勒效应传感器等,实时监测工件的加工精度和尺寸变化,及时发现并纠正加工偏差。
成品检测:加工完成后,对工件进行全面的检测,包括尺寸精度、形状精度、表面粗糙度等方面的检测。使用高精度的测量工具和仪器,如三坐标测量仪、粗糙度仪等,确保工件符合设计要求。
综上所述,CNC加工技术的要求是多方面的,需要在各个环节都严格把控,才能保证加工出的零件或产品符合质量标准,满足各种应用的需求。