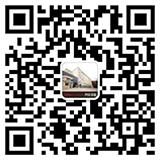
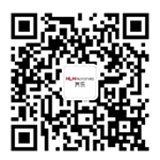
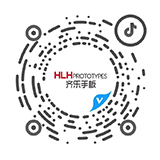



2025-01-20 13:28:37
编程与工艺规划
合理划分工序:可按刀具集中分序法、加工部位分序法、粗精加工分序法等进行。如用同一把刀具加工完零件上所有可完成的部位,减少换刀次数和空程时间;对于复杂零件,按内形、外形、曲面或平面等结构特点划分加工部分,并遵循先平面后孔、先简单后复杂、先粗后精的原则。在划分工序时,要综合考虑零件结构、工艺性、机床功能、加工内容、安装次数及生产组织状况等因素,灵活掌握工序集中或分散原则,力求合理。
优化加工顺序:根据零件结构和毛坯状况以及定位夹紧的需要来安排,重点保证工件刚性不被破坏。应先进行内形内腔加工,后进行外形加工;以相同定位、夹紧方式或同一把刀加工的工序尽量连接进行;在同一次安装中,先安排对工件刚性破坏小的工序。
精准确定对刀点:对刀点应设在基准位或已精加工过的部位,若第一道工序后对刀点被加工毁坏,需在与定位基准有相对固定尺寸关系的地方设立相对对刀位置。选择对刀点时,要考虑找正容易、编程方便、对刀误差小、加工时检查方便可查等因素。同时,工件坐标系由操作者设定,在工件装夹完毕后通过对刀确定,且工件坐标系与编程坐标系必须统一。
科学选择走刀路线:要保证零件的加工精度要求,方便数值计算,减少编程工作量,寻求最短加工路线以提高加工效率,尽量减少程序段数。此外,要确保工件轮廓表面加工后的粗糙度要求,最终轮廓应安排最后一走刀连续加工出来,并认真考虑刀具的进退刀路线,避免在轮廓处停刀留下刀痕或垂直下刀划伤工件。
合理编制加工程序单:加工程序单是数控加工工艺设计的重要内容之一,应包括绘图和编程文件名、工件名称、装夹草图、程序名、每个程序所使用的刀具、切削的最大深度、加工性质(粗加工还是精加工)、理论加工时间等信息,让操作者明确程序内容、装夹和定位方式以及各加工程序所选用的刀具和应注意的问题。
刀具与切削参数选择
刀具选择:根据不同的加工部位和要求选择合适的刀具。例如,平面铣削时选用不重磨硬质合金端铣刀或立铣刀;立铣刀和镶硬质合金刀片的端铣刀主要用于加工凸台、凹槽和箱口面;球刀、圆刀常用于加工曲面和变斜角轮廓外形,其中球刀多用于半精加工和精加工,镶硬质合金刀具的圆刀多用于开粗。
切削参数确定:切削用量包括切削速度、进给量和切削深度等要素。粗加工时,以保证刀具强度和机床功率为前提,优先选取尽可能大的切削深度,其次选择较大的进给量,最后根据刀具寿命和机床功率确定合适的切削速度;精加工时,则主要考虑工件的加工精度和表面质量,通常选取较小的切削深度和进给量,较高的切削速度。
工件装夹与定位
装夹方式选择:力求设计、工艺与编程计算的基准统一;尽量减少装夹次数,争取一次定位后能加工出全部待加工表面;避免采用占机人工调整方案;夹具要开畅,其定位、夹紧机构不能影响加工中的走刀,如产生碰撞,可采用虎钳或加底板抽螺丝的方式装夹。
定位基准确定:定位基准应尽量选择工件上平整、稳定、精度高的表面,以确保工件在加工过程中的位置准确性和重复定位精度。同时,要考虑到后续工序的加工余量和装夹方便性,避免因基准选择不当导致加工误差或无法完成某些部位的加工。
加工过程监控与调整
加工过程监控:在自动加工过程中,操作者要密切监控切削负荷情况,通过切削负荷表观察自动加工过程中的切削负荷变化,根据刀具承受力状况及时调整切削用量,发挥机床的最大效率。同时,要注意监听切削声音,正常情况下,切削声音应是稳定的、连续的、轻快的,若出现不稳定或异常声音,应及时调整切削用量及切削条件,必要时暂停机床检查刀具及工件状况。
精加工监控:精加工时着重注意积屑瘤对加工表面的影响,对于型腔加工还需注意拐角处加工过切与让刀问题。可通过调整切削液的喷淋位置,使加工表面时刻处于冷却条件,并观察工件已加工面质量,通过调整切削用量尽量避免质量变化。若调整无效,则应停机检查原程序是否合理。
刀具监控:刀具的质量对工件加工质量有很大影响,在自动加工切削过程中,要通过声音监控、切削时间控制、切削过程中暂停检查、工件表面分析等方法判断刀具的正常磨损状况及非正常破损状况,并根据加工要求及时处理刀具,防止产生加工质量问题。
机床维护与保养
日常清洁:定期清理机床表面的灰尘、油污和切屑,保持机床的清洁卫生,防止杂物进入机床内部影响其正常运行。特别是导轨、丝杠、工作台等关键部位,要使用合适的清洁剂和工具进行仔细清洁。
润滑保养:按照机床的使用说明书和润滑图表,定期对机床的各个润滑部位进行润滑,如导轨、丝杠、主轴等,确保润滑油的充足和质量良好,减少机床部件的磨损,延长机床的使用寿命。
精度检查与调整:定期对机床的精度进行检查,包括定位精度、重复定位精度、垂直度、平行度等,及时发现并调整机床的精度偏差,保证加工精度的稳定性。对于精度超差的机床,要及时进行维修或送专业厂.家进行调整。
故障排除:操作人员要熟悉机床的基本结构和工作原理,能够识别常见的故障现象,并掌握一些基本的故障排除方法。在机床出现故障时,要及时停机检查,避免故障扩大化,并根据故障情况采取相应的维修措施或联系专业维修人员进行处理。