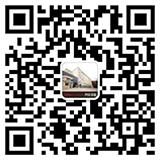
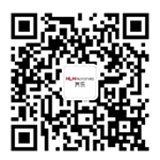
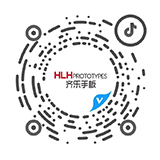



2024-09-26 13:59:43
数控加工过程中容易出现的问题有很多,以下是一些常见的问题及其解决方法:
工件过切原因:刀具强度不够、操作不当、切削余量不均匀以及切削参数不当都可能导致工件过切。改善:选择适当的刀具原则,确保余量均匀,合理调整切削参数,利用机床的SF功能微调速度。
分中问题原因:操作员手动操作不准确、模具周边有毛刺、分中棒有磁以及模具四边不垂直都可能导致分中问题。改善:反复检查手动操作,去除模具周边毛刺,使用无磁分中棒,校表检查模具四边垂直度。
对刀问题原因:操作员手动操作不准确、刀具装夹有误、飞刀上刀片有误差以及R刀与平底刀及飞刀之间的误差都可能导致对刀问题。改善:仔细检查手动操作,确保刀具装夹正确,定期更换刀片,单独出一条对刀程序以避免误差。
撞机问题(编程)原因:安全高度不够或未设置、程序单上的刀具和实际程序刀具写错、程序单上的刀具长度和实际加工深度写错、程序单上深度Z轴取数和实际Z轴取数写错以及编程时座标设置错误都可能导致撞机问题。改善:准确测量工件高度并确保安全高度在工件之上,确保程序单上的刀具和实际程序刀具一致,对实际在工件上加工的深度进行测量并在程序单上写清楚。
撞机问题(操作员)原因:深度Z轴对刀错误、分中碰数及操数错误、用错刀、程序走错以及手动操作时手轮摇错了方向都可能导致撞机问题。改善:注意深度Z轴对刀位置,反复检查分中碰数及操数,装夹刀具时要反复对照程序单检查,程序要一条一条按顺序走,提高机床操作熟练度。
曲面精度问题原因:切削参数不合理、刀具刃口不锋利、刀具装夹太长、排屑不良、编程走刀方式不当以及工件有毛刺都可能导致曲面精度问题。改善:合理设置切削参数和公差余量,定期检查和更换刀具,尽量使刀具装夹短,优化编程走刀方式,了解机床性能并对有毛刺的边进行补刀。
崩刃问题原因:进给太快、切削开始时进给太快、夹紧松(刀具或工件)、刚性不足(刀具)等都可能导致崩刃问题。改善:减慢进给速度,切削开始时减慢进给速度,确保刀具和工件夹紧,使用允许的最短刀具并深夹柄部。
总的来说,数控加工过程中容易出现的问题多种多样,但通过合理的操作、准确的编程和及时的维护,可以有效避免这些问题的发生。