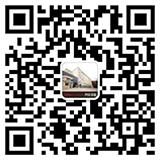
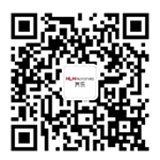
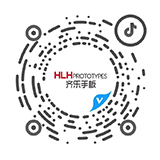



2022-07-06 16:19:03
7月5日消息,近日,Lufthansa Technik(汉莎航空)与Premium AEROTEC联手开发了世界上第一个获准在飞机上使用的3D打印承重金属部件。这款金属3D打印部件专为IAE-V2500发动机的防冰系统设计,现已获得EASA的官方航空认证。
该部件被称为“A-Link”,总共有九个这样的A-Link在发动机的进气口罩上固定了一个环形热空气管道,从而保护它免受结冰。 这些A形连杆之前使用传统的锻造工艺,由钛制成,温度通常高达300°C。但由于发生的振动,这些A-Link通常会在其安装孔处磨损,因此每隔几年就需要更换一次。
现在,Premium AEROTEC和Lufthansa Technik采用激光粉末床融合 (LPBF) 技术,生产时不需要夹具或模具。此外,该过程还可以节省材料,甚至降低了总体制造成本。
为了验证A-Link工艺,Premium AEROTEC使用原型样本进行了“大量”打印测试,最终建立了一个稳定可靠的工艺,并证明能达到对材料性能的最高要求。 在抗拉强度方面,3D打印的A-Link甚至优于原始部件。
“Premium AEROTEC是航空部件增材制造的国际先驱和技术领导者。自2016年以来,我们公司已经将该技术应用于复杂结构部件的批量生产。我很高兴与 Lufthansa Technik合作,再次展示我们在3D打印方面的全面专业知识,”Premium AEROTEC首席运营官Ulrich Weber说。
“多年来,我们一直在使用3D打印为飞机机舱生产部件,其中绝大多数是塑料制成的。现在,我们能够证明在机舱外使用金属相关的结构部件也可以通过增材制造并获准用于飞行操作。通过这种方式,我们不仅节省了相关组件的成本,而且还定义并验证了通过3D打印工艺制作这类部件的所有必要流程,”Lufthansa Technik首席运营官Soeren Stark说。
第一个承重部件是一个巨大的进步,首次航空认证目前仅代表双方合作的第一步。未来,还将使利用增材制造的优势对几何进行有针对性的优化,最终可以使用更少的材料,在保持相同的强度和功能的情况下更容易地生产。